Automated Inspection System Overview
This gallery showcases the early conceptual work on the Automated Inspection System, initially developed to explore offline handling and verification of barcodes and QR codes on pharmaceutical inserts and outserts. The concept focused on automating the feeding and inspection process to improve the reliability of digital code verification without relying on manual checks. While the system later evolved into a fully inline solution, these early designs laid the groundwork for key inspection functionality.
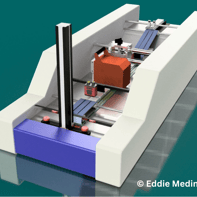
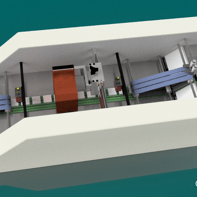
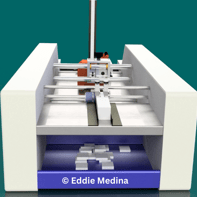
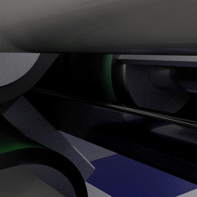
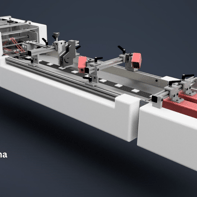
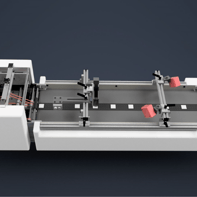
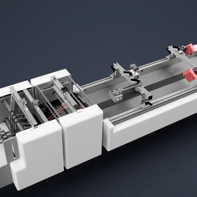
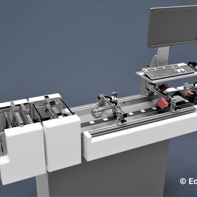
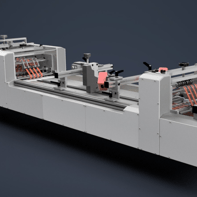
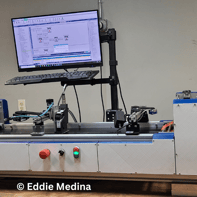
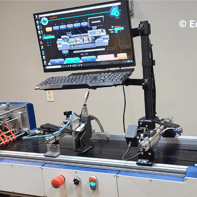
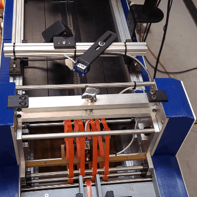
Gallery 2: Dimensional QC
In this phase, the system evolved beyond barcode verification to include dimensional quality control, driven by customer requirements. AI-powered cameras were introduced to detect variations in fold alignment and paper size, ensuring that pharmaceutical inserts remained within strict production tolerances. This marked a significant expansion in the system's inspection capabilities, transitioning it toward a more comprehensive quality assurance solution.
Gallery 3: First Prototype
This gallery marks the transition from concept to functional prototype. The first full build combined barcode and QR code verification with early physical inspection features, including an integrated AI camera system. These images document the hands-on development and real-world testing that validated the system’s core inspection logic and modular design.
Welcome to the Automated Inspection System — a fully modular, inline quality control solution developed to meet the stringent demands of pharmaceutical manufacturing. I led the mechanical design, prototyping, and system integration, collaborating with a software engineer to unify real-time barcode verification, skew correction, glue detection, and dimensional tolerance checks.
The complete system includes the Hugger (skew correction), Curing, Inspection, Reject, and Vertical Stacker modules — each engineered to solve specific production challenges while improving reliability and throughput.
This page details the system’s evolution from early concept and functional prototypes to a fully integrated, production-ready solution. Explore how modular design and smart automation can transform pharmaceutical quality control.
Gallery 1: Early Concepts
Evolution of Innovation: From Initial Concept to Advanced Prototype


This section demonstrates the system’s evolution from digital code verification to full physical inspection capabilities. In response to customer feedback, I expanded the design to detect dimensional inconsistencies and verify adhesive application — ensuring inserts were not only labeled correctly but also folded, glued, and sized within tolerance.
These videos show the prototype successfully inspecting pharmaceutical inserts of various dimensions, including automatic rejection of unglued pieces. This phase confirmed that my modular system could handle real-world variability and meet the stringent quality control standards expected in pharmaceutical production.

Prototype Inspection: Processing 1"x1"x.25" inserts
Prototype Inspection: Inspecting for unglued inserts.
Prototype Inspection: Processing 2"x1"x.30" inserts
Final Prototype Unveiled: Integrated Inspection System


This final prototype represents a complete, operational integration of all major modules — including Hugger, Curing, Inspection, Reject, and Stacker. It demonstrates not only mechanical functionality but the coordinated interaction between components that ensures reliable pharmaceutical inspection at production speed. These videos and images show the system in action, validating its performance through real-time operation and physical testing.
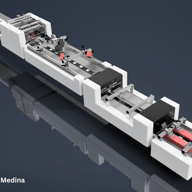
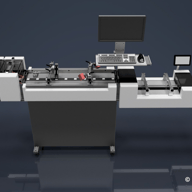
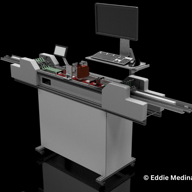
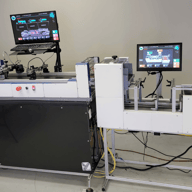
Complete Prototype System: An Overview
Prototype Curing Module in Action.
This gallery illustrates the prototype’s evolution from initial conceptual renderings to full mechanical assembly, highlighting key stages in the design-to-build process.
Complete System Overview: Practical Modular Integration

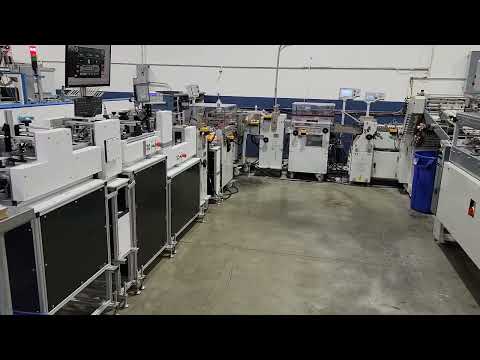
The final installed system marks the successful transition from prototype to production-ready machinery. Designed, built, and tested to meet real-world pharmaceutical manufacturing requirements, this modular inspection solution integrates barcode verification, dimensional accuracy checks, adhesive curing, and reject handling into a cohesive inline process.
Its seamless operation in a live production environment confirms the reliability of both the mechanical design and integrated control systems. This outcome reflects my ability to take complex automation challenges from concept to deployment, delivering robust, adaptable solutions that meet high standards for quality and performance.
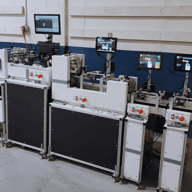
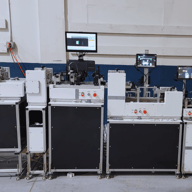
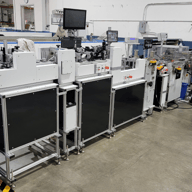
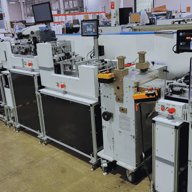
Gallery: The fully installed system, shown in its production-ready form, including real-world layout and final mechanical integration.
Complete System Running Online.
Installed System - Overview.
This conceptual rendering illustrates a future expansion of the system: integrating the inspection platform with a fully automated tray-forming and packaging unit. The proposed Auto Tray Packer Former receives stacks of inspected inserts and outserts, then forms flat tray blanks around them in-line — eliminating the need for pre-formed boxes or separate packaging machinery.
This design aims to streamline production by automating both inspection and packaging in a single workflow. By removing manual handling and reducing the number of required machines, it offers the potential to lower labor costs, improve throughput, and increase quality control consistency. While not yet built, this concept reflects my continued focus on scalable, high-efficiency solutions for pharmaceutical manufacturing.
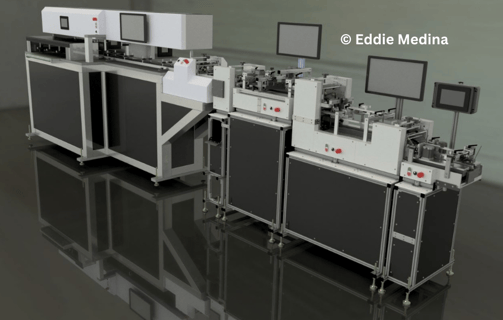
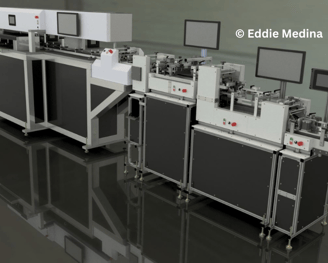