Curing Module: Ensuring Adhesive Integrity for Quality Control
The Curing Module is a critical component engineered to ensure proper adhesive curing in high-speed pharmaceutical production. Inserts are stacked vertically under controlled pressure, creating a timed environment where adhesives can dry effectively—typically requiring 20 seconds of dwell time.
Designed to match the folder’s maximum output speed, the module maintains continuous production flow while eliminating the need for manual intervention. Once cured, inserts are seamlessly transferred to the Inspection Module for barcode and glue verification.
From concept to deployment, this system showcases how targeted mechanical design can solve specific production challenges—boosting efficiency, ensuring adhesive integrity, and reducing waste in demanding manufacturing environments.
Explore the initial design concepts of the Curing Module, where early renderings illustrate the foundational ideas behind its vertical stacking and adhesive curing strategy. These images represent the starting point for a solution focused on maintaining speed, pressure, and curing time within pharmaceutical production.
Gallery 1: Conceptual Beginnings
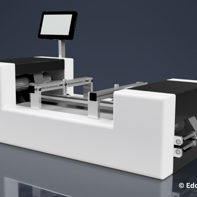

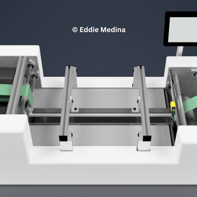
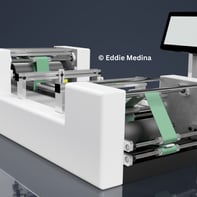
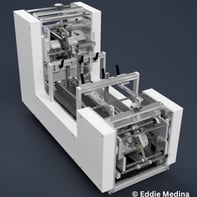
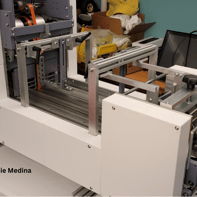
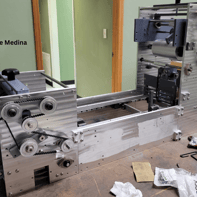
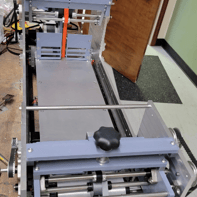
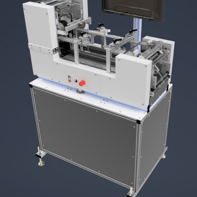
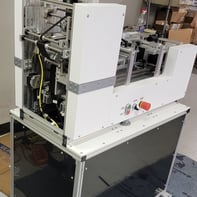
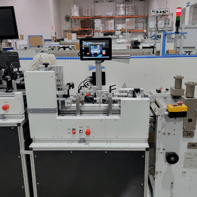
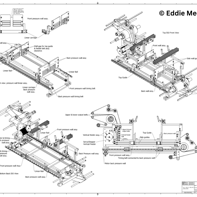
Gallery 2: Concept to Prototype
This gallery captures the evolution of the Curing Module into its first functional prototype. From early renderings to the assembled physical unit, these images show the transition from concept to reality—highlighting the initial engineering decisions that shaped the module’s development.
Gallery 3: Final Outcome
This gallery presents the completed Curing Module, from final design renderings to real-world deployment. These images showcase the module as it appears fully integrated within the inspection system, along with technical drawings that supported the patent process—underscoring the precision and engineering behind the final build.
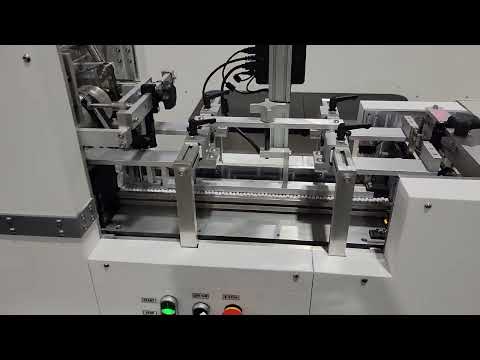

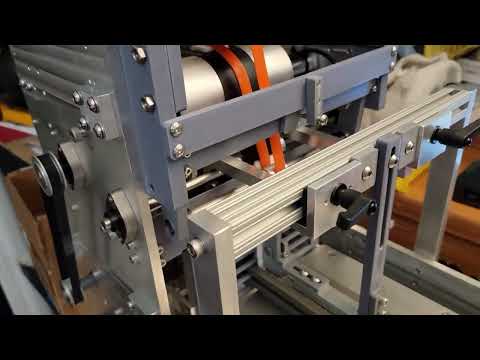
Prototype GUI-Controlled Empty Sequence Demonstration
Prototype Demonstration of Synchronized Feed and Cure Timing
End-of-Job Ejection: Clearing the Curing Module for Batch Completion
Final Curing Module in Continuous Operation

Demonstrates the automatic ejection of remaining inserts at the end of a production run using the Curing Module’s emptying feature—ensuring clean transitions between jobs without manual intervention.
Watch the production-ready Curing Module in action, operating at full capacity. Inserts are held under pressure for timed adhesive curing while flowing seamlessly from the feeder into the inspection system.
This video shows the early-stage prototype of the Curing Module executing the empty sequence via its custom PLC interface. It highlights how the GUI was used to manually trigger and test system functionality during development.
This video captures the curing module prototype in a live synchronization test. As the feeder delivers an insert, the system ejects one cured insert in response—demonstrating the precise timing logic that maintains consistent curing intervals and inline balance.